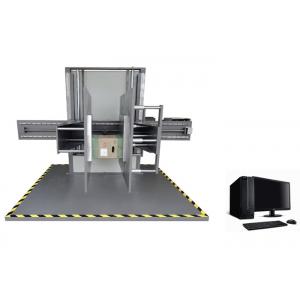
Add to Cart
Product Packaging Clamping Testing Machine For Packaging Testing And Verification
Product overview:
This machine mainly focuses on the ability of the product to withstand the pressure from the vehicle lead after being packaged and loaded and unloaded in the warehouse, truck, train, etc., thereby assessing the damage to the product.
The entire machine is controlled by servo motor, fully computer-operated, and equipped with high-end equipment.
Testing is conducted in accordance with ASTM D6055, US, SEARS, corporate standards or customized according to customer-specified non-standard requirements.
Applicable to all product packaging testing and verification. It mainly tests the deformation of product packaging when it is subjected to horizontal pressure during transportation and storage and the ability of the packaging to protect the inner packaging, thereby improving the packaging design.
Control requirements:
1. Computer control: full computer automatic control software
2. Curve generation: clamping force, pressure, displacement
3. Data: maximum clamping force, pressure, displacement, times, maximum value, minimum value, average value.
4. Report output: Automatically generate a report with curves attached.
5. Curve export: generate reports in word or excel format
Test process:
1. Software settings: Set the force value on the computer software, the movement rate of the clamping plate close to the test sample, the clamping force application speed, the force application time, the force compression amount (0~100mm, accuracy ±0.5mm) limit value, weight rising height, rising/falling speed, pause time, and total number of tests.
2. Test method: Place the tested sample between the two clamping plates according to the test standard (it may be at any position, such as a bottom corner), and start the computer software. The equipment automatically performs actions such as clamping, force maintenance, rising, stopping, falling to 0 point, releasing, etc. This is a test.
3. Determination: When the force value starts to rise, start counting the amount of product compression. When the limit value is exceeded, the test automatically stops, the equipment needs to be reset by personnel, and the computer software records the corresponding data and test results.
Technical parameters:
Sample shape | Parallelopiped transport packaging |
Maximum test weight | 100kg |
clamping pressure | According to the handling diagram on the test sample, a pressure of 400~3000Lb (adjustable) can be applied to the corresponding surface. |
Clamping board size | 1000 × 1000mm (length and width) |
Test space size | 1000 × 1000 × 1000mm (length, width and height) |
Clamping plate height adjustment | 0-1000mm can be set |
Lifting speed | 10-50mm/min adjustable |
clamping speed | 10-50mm/min adjustable |
Plywood telescopic width | 200 ~ 2000mm |
transfer method | Servo motor (left and right clamping) |
Base plate size | 2000 × 1900mm |
protective device | Leakage protection limit device |
Splint requirements |
|
force accuracy | National standard 1.6 level |
operate | The manual operating lever simulates the actual operation of a forklift to control clamping, opening, raising and lowering movements. |
Power supply | AC220V, 50HZ |
Environmental requirements:
1. On-site temperature: 5℃~+28℃ (average temperature within 24 hours ≤28℃);
2. Relative humidity: ≤85%RH;
3. Power supply conditions: single-phase three-wire;
4. Voltage range: AC220V;
5. Allowable frequency fluctuation range: (50±0.5)Hz;
6. The grounding resistance of the protective ground wire is less than 4Ω;
7. The user is required to configure an air or power switch of corresponding capacity for the equipment at the installation site, and this switch must be independent for use by the equipment.